Korrekter Umgang
Die richtige
Seilinspektion
Warum Seilinspektion?
Bei Seilen in Seiltrieben handelt es sich um offene Getriebe, die äußeren Einflüssen ausgesetzt sind, aber auch gängige Verschleißerscheinungen haben. Vor allem sind Seile aber auf Ihre Lebensdauer zeitlich begrenzt. Mit Erreichen der Ablegereife hat das Seil auch das Ende seiner Lebensdauer erreicht. Die Ablegereife des Seiles muss rechtzeitig erkannt werden, um Unfälle wie z. B. einen Seilriss zu vermeiden. Diese Erkennung erfordert regelmäßige Seilinspektionen, die dokumentieren, zu wie viel Prozent das verwendete Seil bereits ablegereif ist.
Eine aussagekräftige Seilinspektion sollte folgende Punkte berücksichtigen:
- Allgemeine Sichtkontrolle (Stellen, die erhöhte Aufmerksamkeit erfordern)
- Durchmessermessung mit geeignetem Werkzeug und an verschiedenen Stellen
- Messung der Seilschlaglänge
- Grad der Korrosion beurteilen (falls vorhanden)
- Meist beanspruchte Seilzone auf Drahtbrüche untersuchen und einordnen
- Messen der Rillendurchmesser, die sich im Seiltrieb befinden
- Schmiermittelmenge auf der Seiloberfläche beurteilen
Solche Inspektionen müssen regelmäßig durchgeführt werden, die Intervalle der verschiedenen Punkte dürfen jedoch variieren. Eine Sichtkontrolle sollte täglich stattfinden, jedoch sollte der Durchmesser, je nach Beanspruchung, monatlich oder quartalsweise gemessen werden. Grundsätzlich ist den gängigen Normen wie z. B. der ISO 4309 zu folgen.
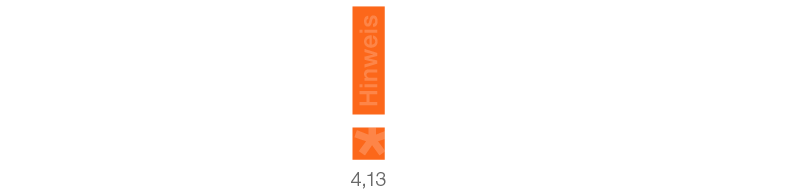
Allgemeine Sichtkontrolle und tägliche Sichtprüfung
Mit einer allgemeinen Sichtkontrolle, welche vom Kranführer durchzuführen ist, sollen offensichtliche Schäden wie z. B. gerissene Litzen oder Fehler in der Einscherung frühzeitig erkannt, und wenn möglich, vor Aufnahme des Betriebs behoben werden.
Hierbei sind Bereiche nahe der Endverbindung und Seilzonen, die mit der Krankonstruktion in Berührung kommen könnten und die Seiltrommel mit erhöhter Aufmerksamkeit zu kontrollieren. Durchzuführen per Sichtkontrolle durch den Kranfahrer.
Regelmäßige Inspektion
Die regelmäßige Inspektion ist von einer fachkundigen Person durchzuführen. Hierbei sollte die komplette Krananlage überwacht und gewartet werden.
Beispiele aus der Praxis
- Messungen, die quartalsweise durchzuführen sind: Durchmesser und Schlaglänge
- Jährliche Messungen: Rillengröße, Seilscheibentiefe, Härte der Seilrollen und Trommel (optional)
Benötigte Werkzeuge für eine Seilinspektion
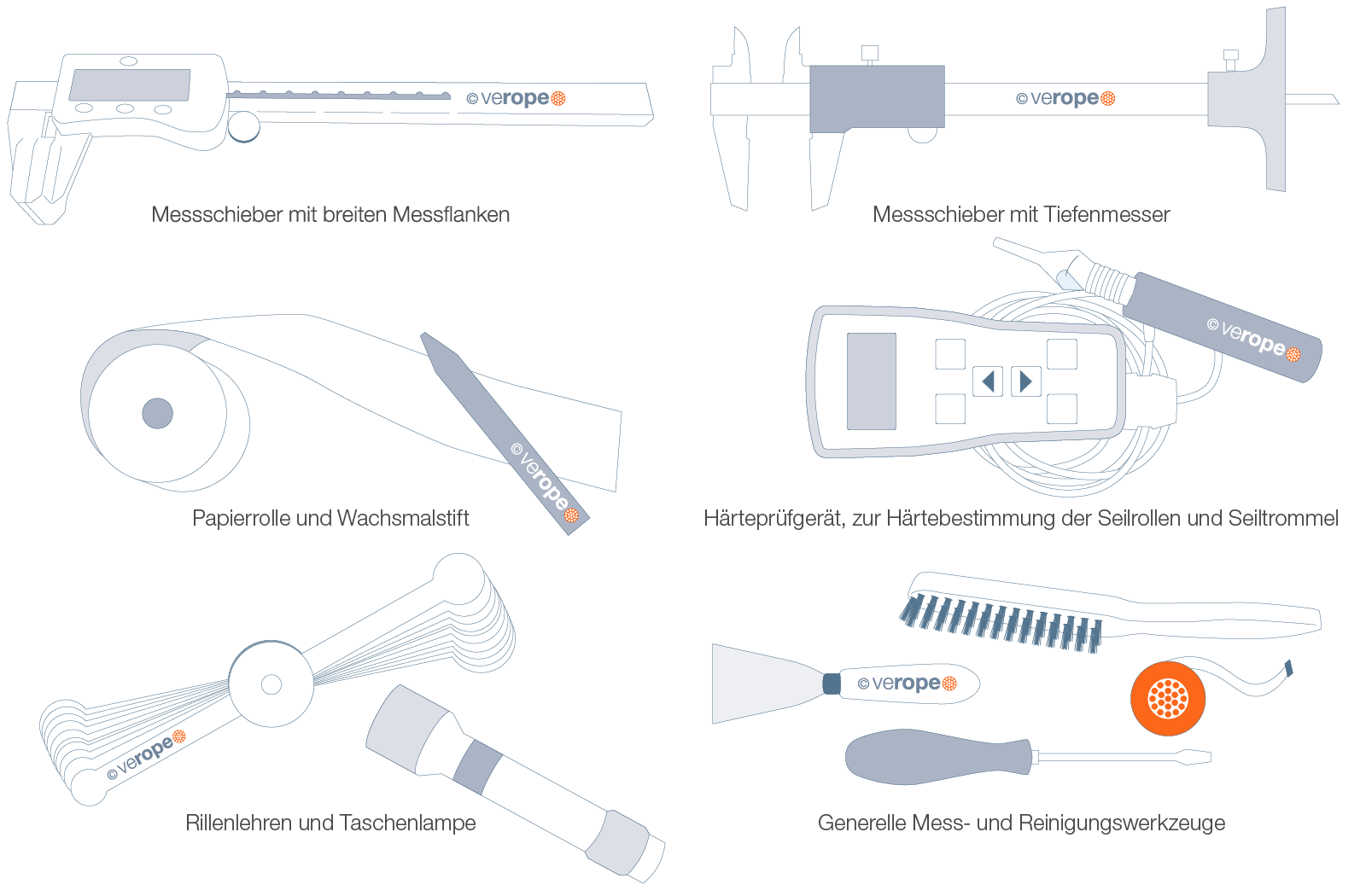
Durchmesser eines Seils messen
Der Durchmesser eines Seiles im laufenden Betrieb gibt Aufschluss über den Verschleiß und die Reduzierung des Durchmessers. So kann aber auch ein erhöhter Durchmesser auf eine Gefügeveränderung zurückzuführen sein. Der Durchmesser des Seiles sollte stets mit geeignetem Messmittel ermittelt werden. Hierbei sind Messschieber mit breiteren Messflanken von Vorteil. Folgende Bilder zeigen geeignete Messmittel:
Ein Seil muss stets an seiner breitesten Stelle gemessen werden, d. h. von Litzenkuppe zu Litzenkuppe: Eine vollständige Messung besteht aus zwei Messungen jeweils in X-Richtung und in Y-Richtung und ca. 1 m voneinander entfernt. Der sich daraus ergebende Mittelwert beschreibt den aktuellen Seildurchmesser.
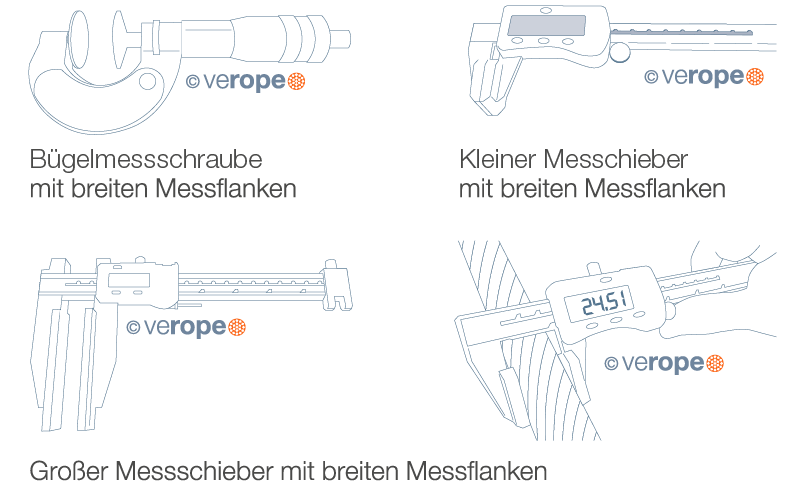
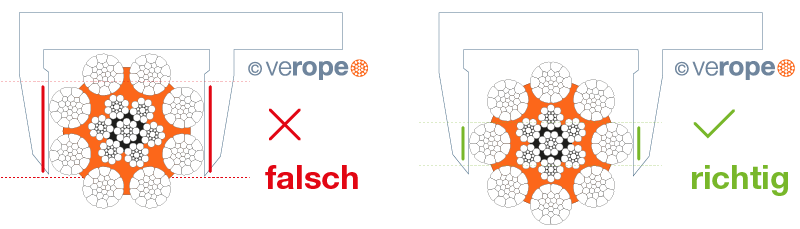

Wie man die Schlaglänge eines Seils misst
Ob ein Seil gewaltsam verdreht wurde bzw. generell eine unnatürliche Verdrehung erfahren hat, lässt sich an der Schlaglänge feststellen. Um die Schlaglänge zu messen, benötigt man folgende Utensilien: Papierstreifen (Kassenrolle), Wachsmalkreide, Lineal, Kugelschreiber. Mithilfe des Papierstreifen und der Wachsmalkreide erzeugt man ein Negativ von der Seiloberfläche. Dazu erzeugt man durch Auflegen des Papieres und Überstreifen (Abpausen) mit Kreide einen Negativabdruck von der Seiloberfläche.
Heraus kommt ein Abdruck der Litzen auf dem Papier. Um nun die Schlaglänge des Seiles zu ermitteln, muss eine bestimmte Anzahl von Abdrücken gezählt werden. Hierbei ist die Anzahl der Außenlitzen entscheidend (im unteren Bild sind es demnach 8 Außenlitzen). Die Distanz von Anfangs- und Endpunkt ergibt die Schlaglänge in mm. Es wird empfohlen, mindestens drei Messungen durchzuzählen und die Gesamtlänge durch drei zu teilen. Damit werden Messfehler reduziert.

Gesamtlänge geteilt durch die Anzahl der Messungen
Messen von Seilrollenprofilen
Zu einer Seilinspektion gehört nicht nur das Untersuchen des Seiles an sich, sondern auch der Seilscheiben, in denen das Seil läuft. Für die Messung der Rillendurchmesser sind besondere Messmittel erforderlich: Verschiedene Rillenlehren und eine Taschenlampe.
Solche Rillenlehren sind auf Anfrage bei verope® erhältlich. Die angegebenen Werte auf der Lehre sind tatsächliche Werte und keine Sollwerte, wie es manchmal üblich ist. Die Taschenlampe dient als Hilfe, um das genaue Maß zu ermitteln. Hierbei wird die Lehre in der Rille von hinten angestrahlt. Ein sichtbarer Lichtschlitz zeigt, dass die genutzte Lehre zu groß oder zu klein ist. Sollte am kompletten Radius der Lehre kein Lichtschlitz mehr zu sehen sein, so wurde das richtige Rillenmaß ermittelt.
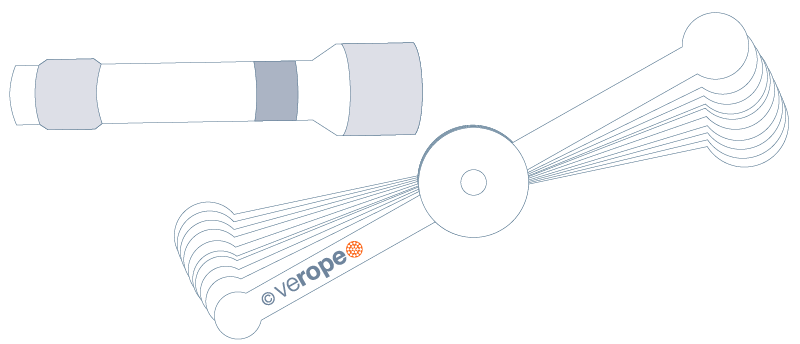
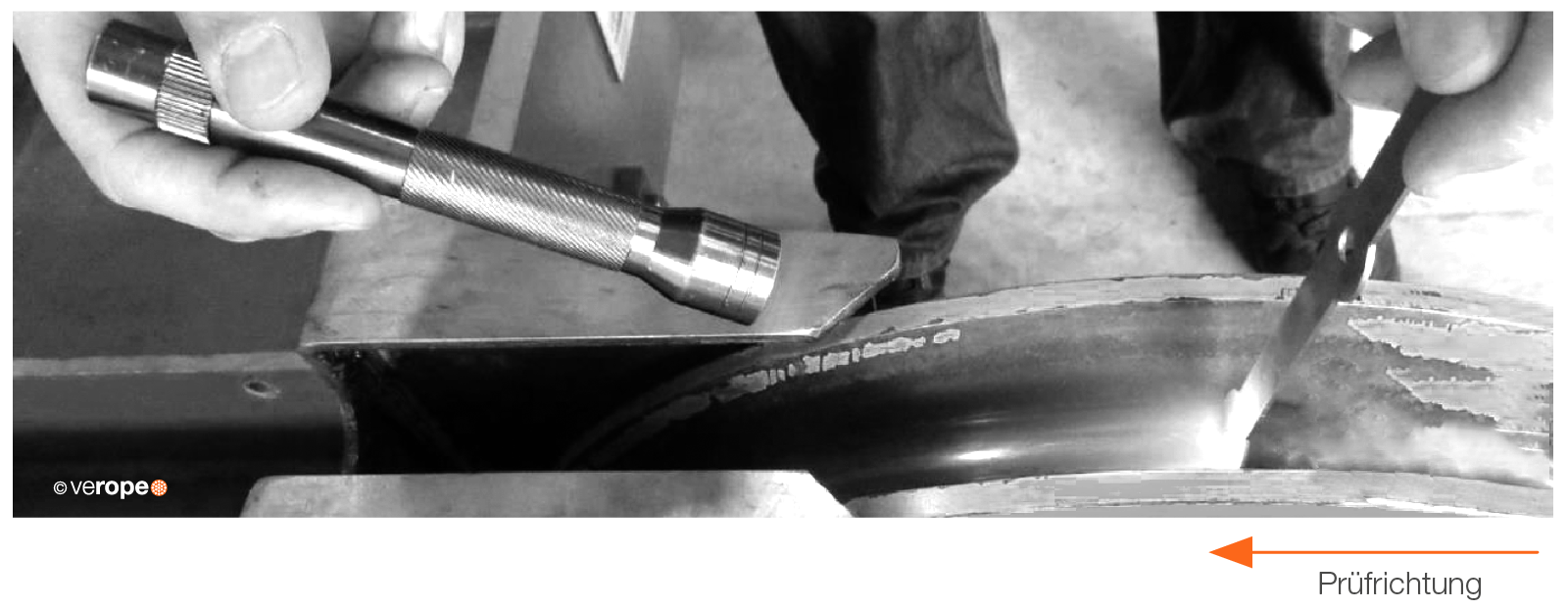
Die folgenden Bilder zeigen die unterschiedlichen Szenarien, die bei der Messung auftreten können.
R = Rillenradius
d = Seilnenndurchmesser
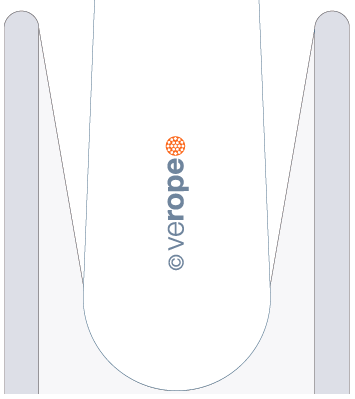
Der Lichtschlitz wird von der kompletten Rillenlehre verdeckt: Lehre hat das Maß des Rillengrunds.
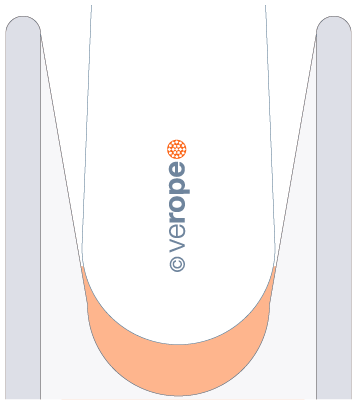
Der Lichtschlitz ist deutlich zu sehen: Die verwendete Rillenlehre ist zu groß.
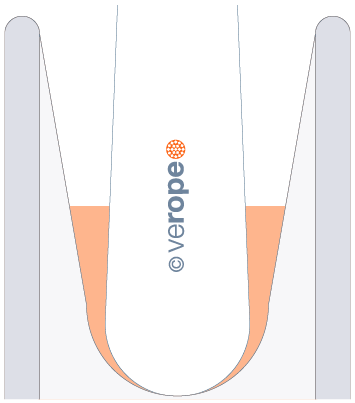
Der Lichtschlitz wird nicht vom kompletten Radius verdeckt: Die Rillenlehre ist zu klein.
Laut Norm sollte der Rillenradius R zwischen 0,525 x d und 0,550 x d liegen, optimal liegt der Rillenradius bei 0,5375 x d.
Beispiel:
Bei einem Seil mit einem nominellen Durchmesser von 22 mm gelten folgende Werte:
- Minimal erlaubter Rillendurchmesser: 23,10 mm
- Optimaler Rillendurchmesser: 23,66 mm
- Maximal erlaubter Rillendurchmesser: 24,20 mm
Das untere Diagramm zeigt die Auswirkung auf die Seillebensdauer bei unterschiedlichen Rillengrößenverhältnissen.
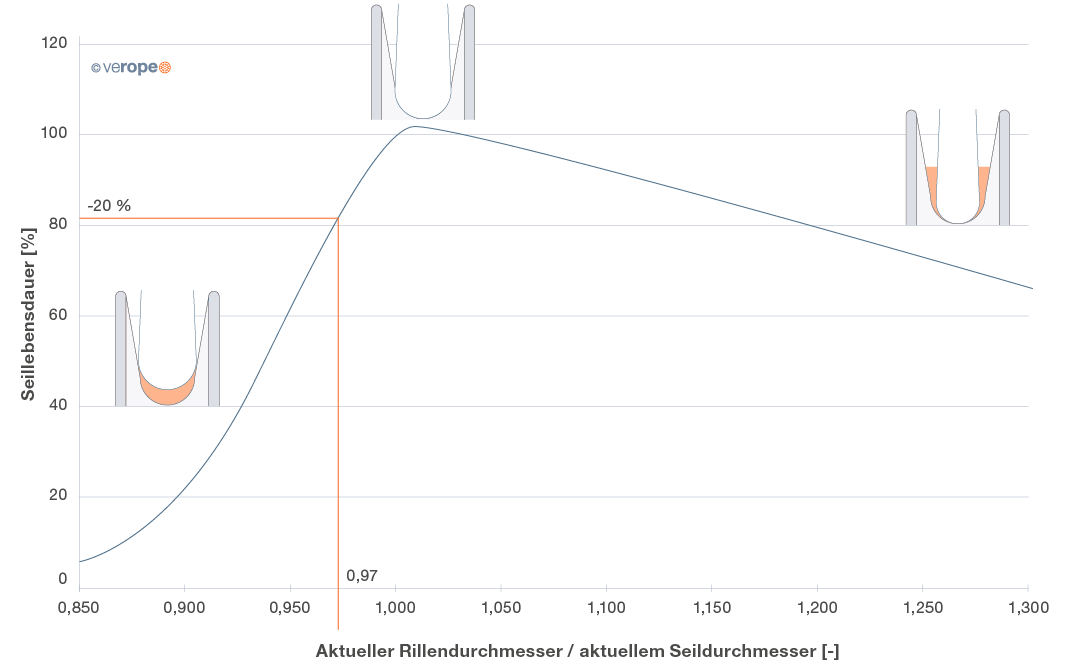
Beispiel:
Ein Seil mit dem Ist-Durchmesser von 22,60 mm, welches in einer Rille mit einem Ist-Durchmesser von 22 mm arbeitet, erfährt ein Lebensdauerverlust von ca. 20 %.
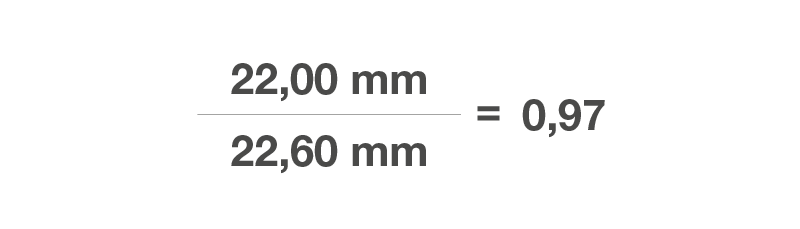
Rillentiefe
Laut ISO 16625 sollte die Rillentiefe nicht größer als das 1,5-fache des Seildurchmessers sein. Darüber hinaus muss der Rillengrund kreisförmig sein. Die maximal zulässige Tiefe, bis zum verschleißbedingten Austausch der Seilscheiben, muss vom Seilscheibenhersteller angegeben, bzw. bei ihm erfragt werden. Dieser Wert ist unbedingt einzuhalten, da durch Missachtung schwere Unfälle infolge des Materialversagens passieren können.
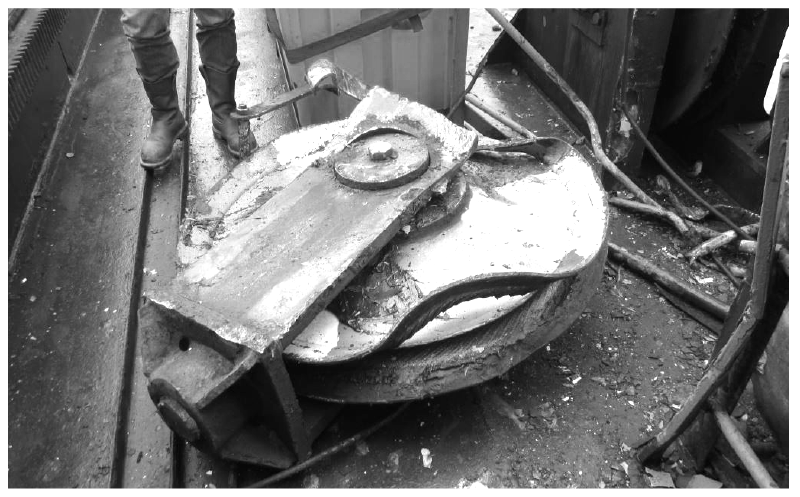
Materialhärte
Seile besitzen in der Regel verschiedene Festigkeiten. So sind Klassen wie 1770 N/mm2, 1960 N/mm2 oder 2160 N/mm2 üblich. Das aufgeführte Diagramm zeigt den jeweiligen Härtegrad in HV (Härte Vickers) zu der dazugehörigen Festigkeitsklasse an. Die Härte der Seilscheibe und Seiltrommel sollte zwischen 300 – 350 HV liegen. Dies wird dadurch begründet, dass zu weiche Seilscheiben den reinen Anlagenverschleiß aufnehmen und dadurch die Ablegereife des Seiles schlechter zu erkennen ist. Sollte die eingesetzte Seilscheibe oder Seiltrommel einen höheren Härtewert aufweisen, ist dies zum Erkennen der Ablegereife unbedenklich, jedoch mit höheren Kosten in der Härtung verbunden.
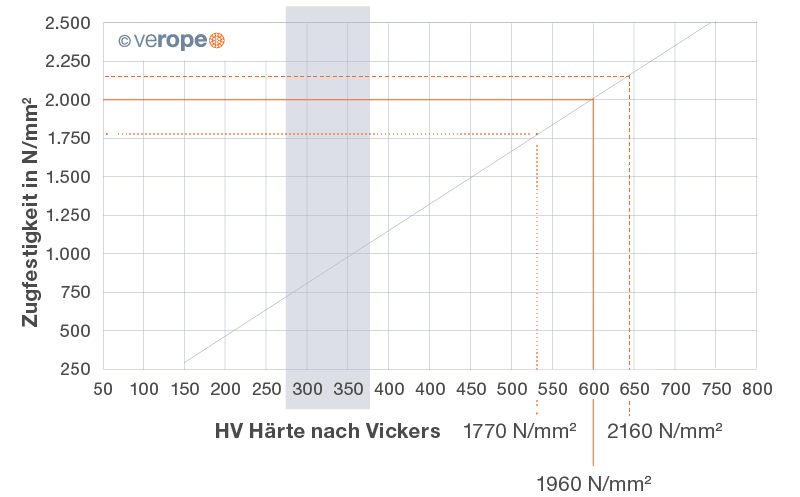
Drahtbrüche auf der Seiloberfläche
Drahtbrüche auf der Seiloberfläche können durch Biegebeanspruchung des Seiles beim Lauf über Seilscheiben oder Verschleiß entstehen.
Die Menge der Drahtbrüche darf auf einer definierten Länge eine gewisse Anzahl nicht überschreiten, sonst hat das Seil seine Ablegereife erreicht.

Drahtbrüche, die durch Biegebeanspruchung hervorgerufen werden, vervielfachen sich zum einen exponentiell und treten zum anderen willkürlich auf.
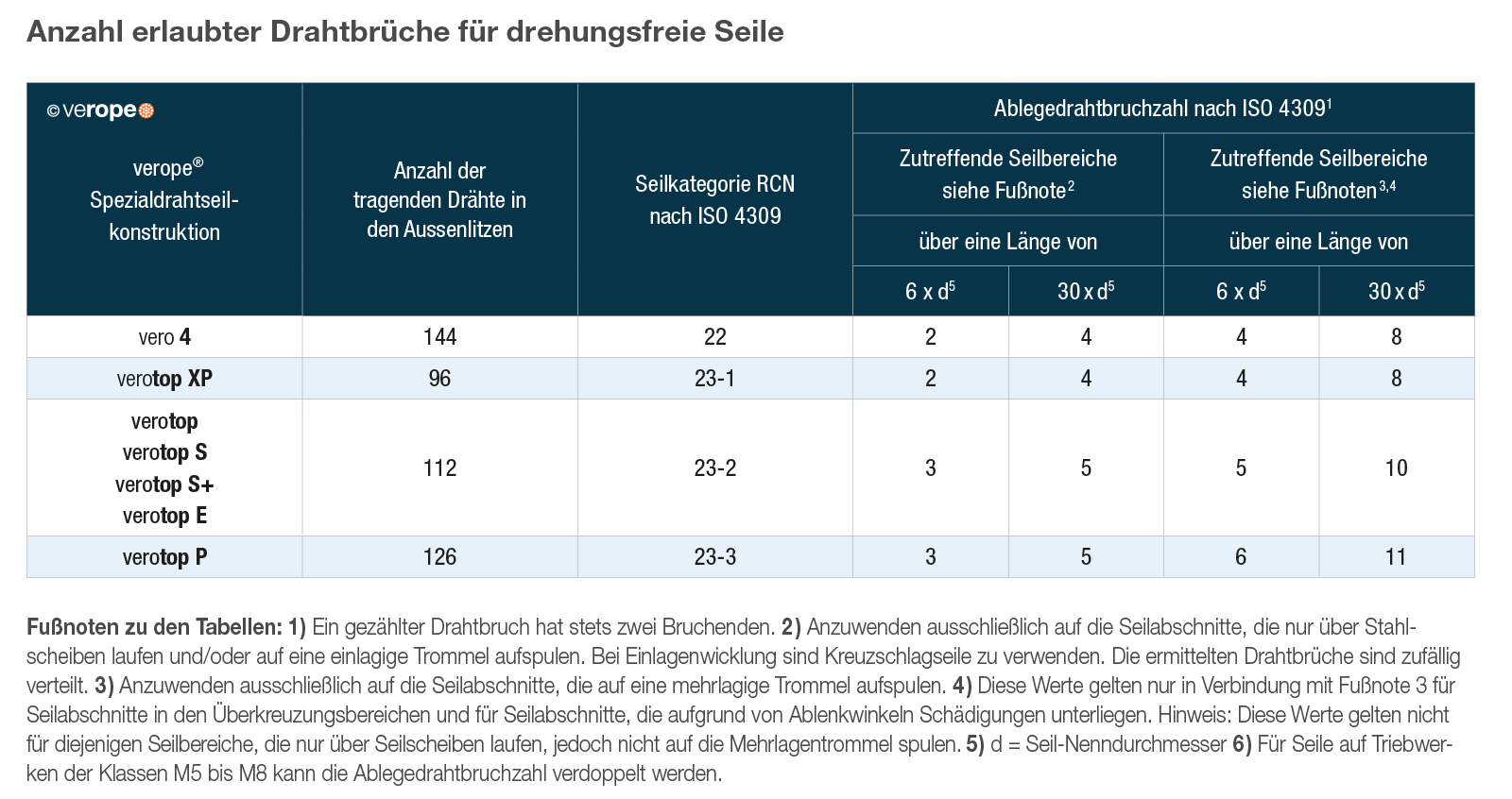
Entfernen von abstehenden Drähten
Bei manchen Drahtbrüchen kann es passieren, dass der gebrochene Draht vom Seil absteht. Dieser Draht kann beim erneuten Lauf über die Seilscheibe benachbarte Drähte beschädigen und somit Sekundärdrahtbrüche hervorrufen. Mit Hilfe einer Zange und kontinuierlichem Hin- und Herbiegen des abstehenden Drahtes kann dieser entfernt werden und stellt für benachbarte Drähte keine Gefahr mehr dar.
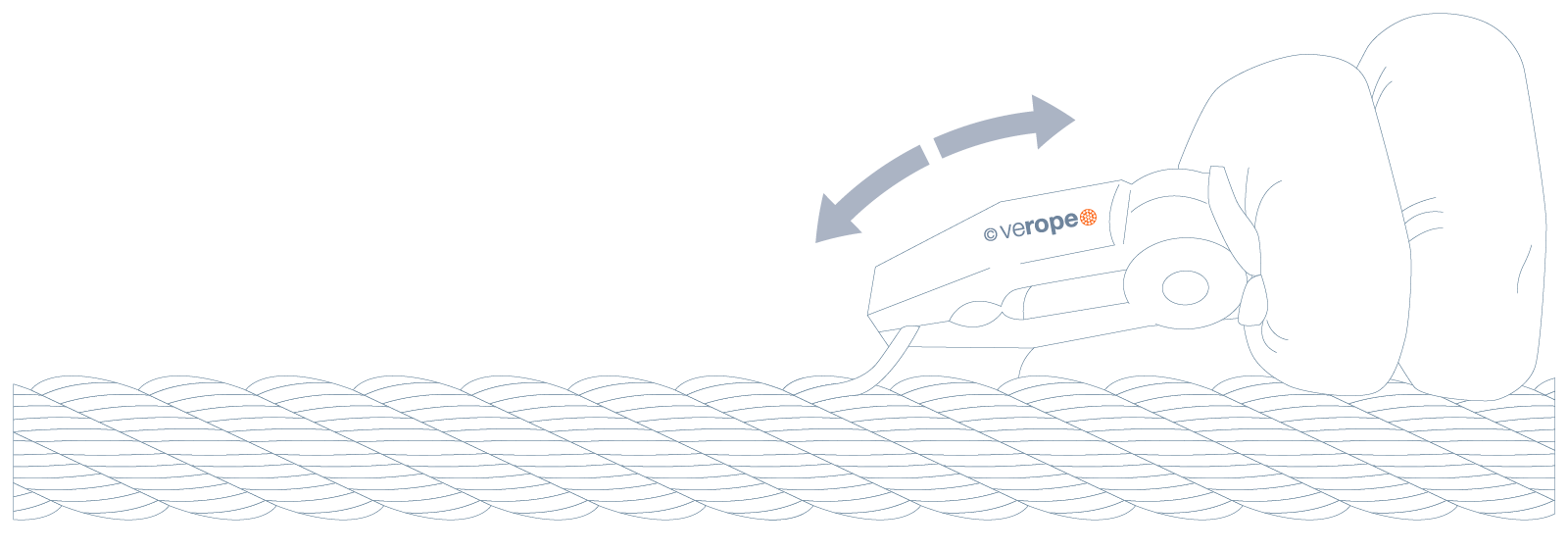
Grad der Seilkorrosion
Seile, die in gewissen Umgebungen arbeiten oder eine erhöhte Standzeit aufweisen, beginnen zu korrodieren. Hierbei wird zwischen verschiedenen Korrosionsgraden unterschieden.
Eine allgemein geltende Unterscheidung bietet die DIN ISO 4309.
Leitlinie zur Beurteilung und Einstufung äußerlicher Korrosion

1. Beginnende Oxidation der Oberfläche, lässt sich abwischen, nur oberflächlich. Einstufung: 0 % der Ablegereife.
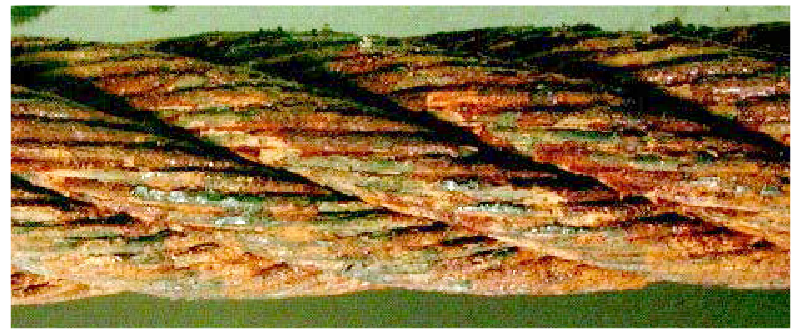
3. Oberfläche stark oxidiert. Einstufung: 60 % der Ablegereife.

2. Drähte fühlen sich rau an, allgemeine Oxidation der Oberfläche. Einstufung: 20 % der Ablegereife.
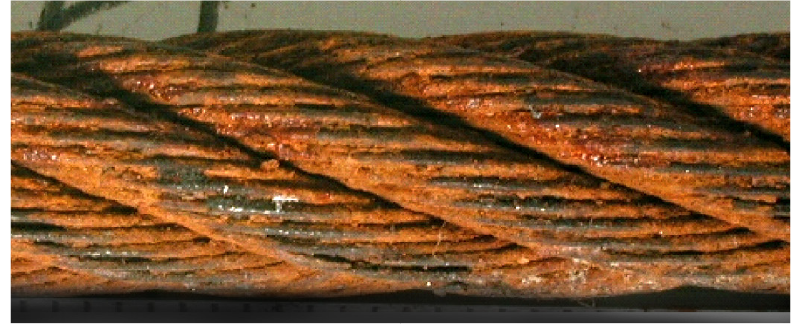
4. Oberfläche stark zerfressen, Drähte spannungslos, Lücken zwischen Drähten. Unverzügliche Ablage.
Durchmesserreduzierung
Der Seildurchmesser eines arbeitenden Seiles reduziert sich über die gesamte Lebensdauer stetig. Diese Reduzierung des Durchmessers ist bedingt durch Abrieb und Verschleiß und wird nach folgender Tabelle bewertet und bis hin zur Ablegereife eingestuft.

Mit folgender Formel wird die Durchmesserreduzierung bestimmt:
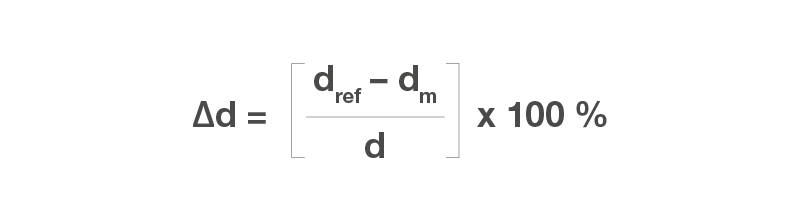
Beispiel:
Ein nicht drehungsfreies Seil mit einem nominellen Durchmesser von 22,00 mm hat einen Referenzdurchmesser (Seildurchmesser im Neuzustand) von 22,80 mm und einen gemessenen Durchmesser von 21,90 mm.
Es gilt:

Das Seil hat zu 20 % die Ablegereife nach Durchmesserreduzierung erreicht.
Inspektionsbericht
Eine hilfreiche Unterstützung bietet der Inspektionsbericht der DIN ISO 4309. In diesem Bericht sind alle relevanten Punkte einer strukturierten Seiluntersuchung aufgeführt.
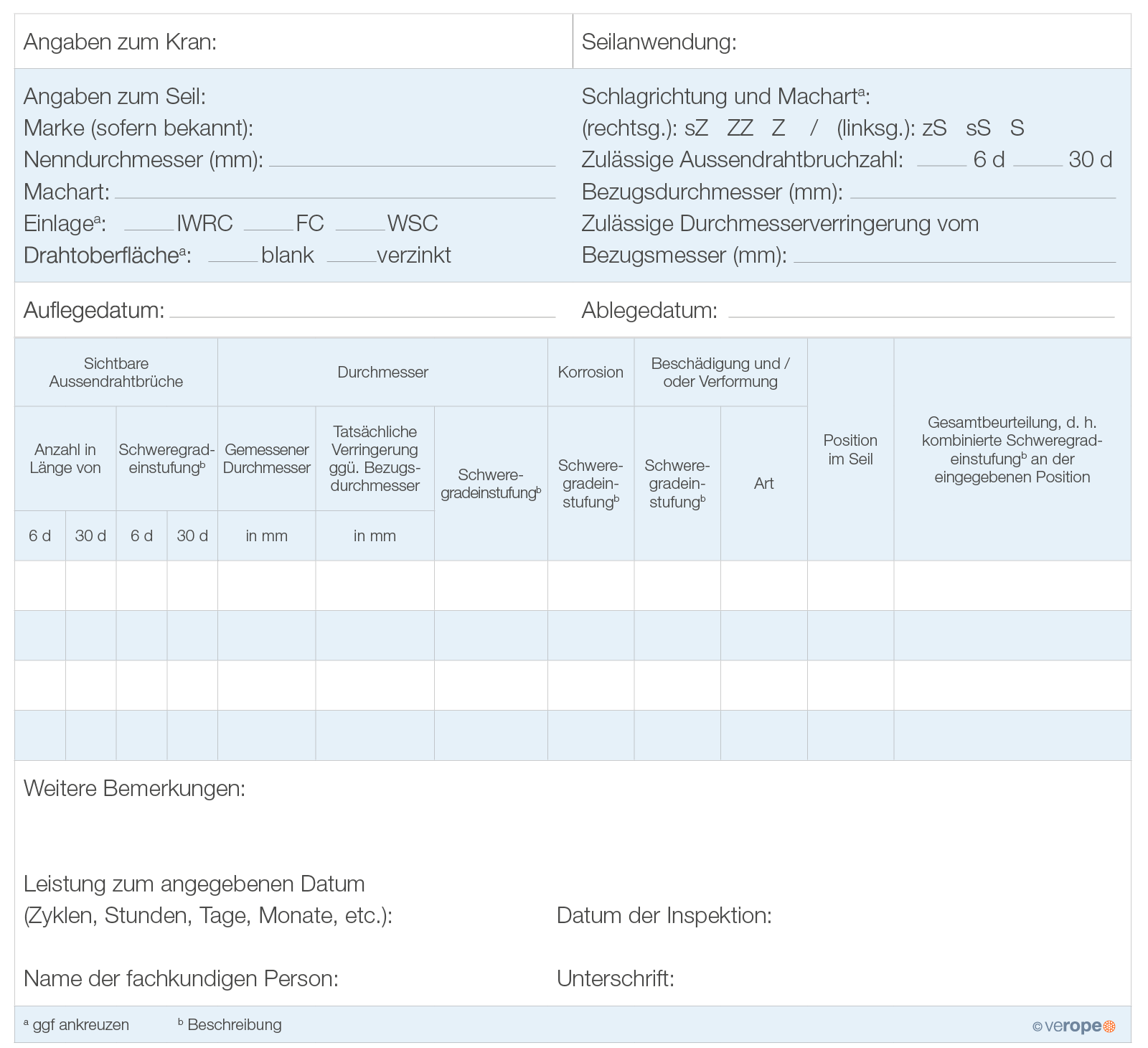
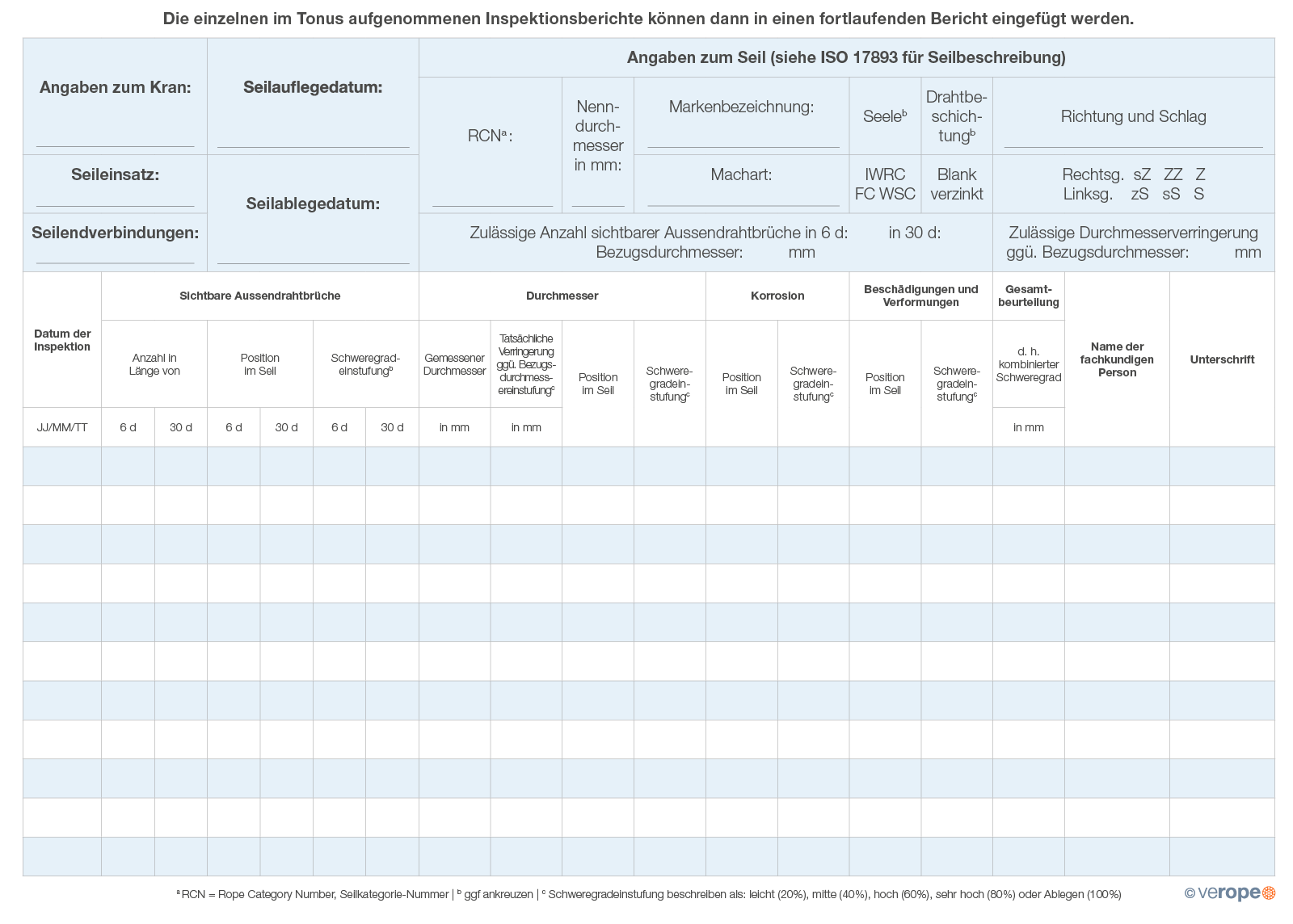
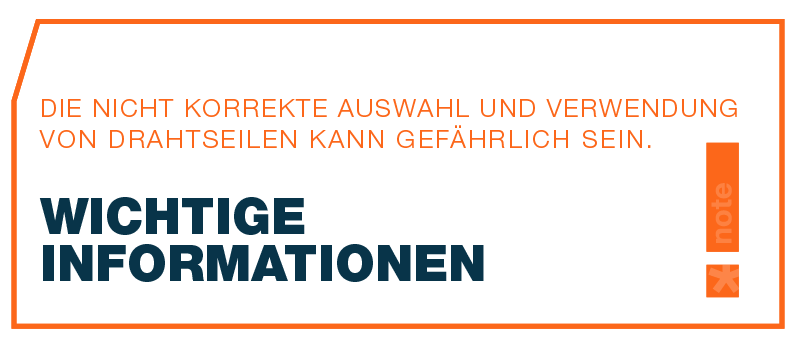
Mit den nachfolgenden Hinweisen möchten wir Sie auf einige wesentliche Punkte für korrekte Auswahl, Betrieb und Überwachung von Drahtseilen aufmerksam machen. Neben technischer Literatur zu Drahtseilen, nationalen und internationalen Normen, steht Ihnen das verope® Team bei allen Fragen rund um das Drahtseil gerne unterstützend zur Verfügung. Bitte sprechen Sie uns an!
Die folgenden Punkte beziehen sich auf die Informationen, die den Hinweisen dieses Artikels nachkommen. Hier finden Sie die Übersicht aller wichtigen Informationen.
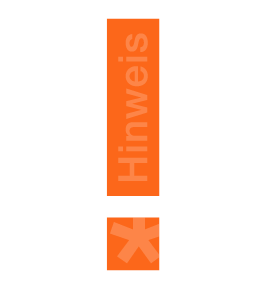
Nr. 4:
Drahtseile und deren Endverbindungen sind nicht dauer-
fest und müssen deshalb für einen betriebssicheren
Zustand regelmäßig inspiziert werden. Drahtseile und deren Endverbindungen müssen vor Erreichen eines unsicheren Zustandes abgelegt werden. Beachten Sie bitte die jeweils gültigen internationalen oder nationalen Normen (z. B. ISO 4309, EN 12385 und EN 13411) und die Fachliteratur zur sachkundigen Inspektion, sowie zur korrekten Ermittlung der Ablegereife von Drahtseilen und deren Endverbindungen. Bei der Installation von Seilen, die mit einer Endverbindung versehen wurden, ist darauf zu achten, dass diese gemäß den Bedienungsvorschriften am vorgesehenen Platz und in der richtigen Position installiert werden. Bei Endverbindungen, die sich demontieren lassen, wie z. B. Keilendklemmen, ist es zwingend notwendig, die vom Seil- bzw. Endverbindungshersteller angegebenen Nenngrößenpaare einzuhalten.
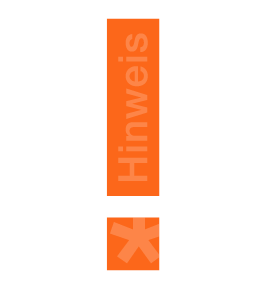
Nr. 13:
Die Abstände zwischen den regelmäßigen Inspektionen sind in Abhängigkeit des Zustandes, der Intensität und den äußeren Einwirkungen der Anlage festzulegen
Bei Fragen, Unklarheiten oder Problemen kontaktieren Sie bitte den Technischen Kundenservice von verope®: TCS@verope.com
Schützen Sie sich und Andere!
Seilversagen kann schwere Sachschäden, Verletzungen oder Tod verursachen!